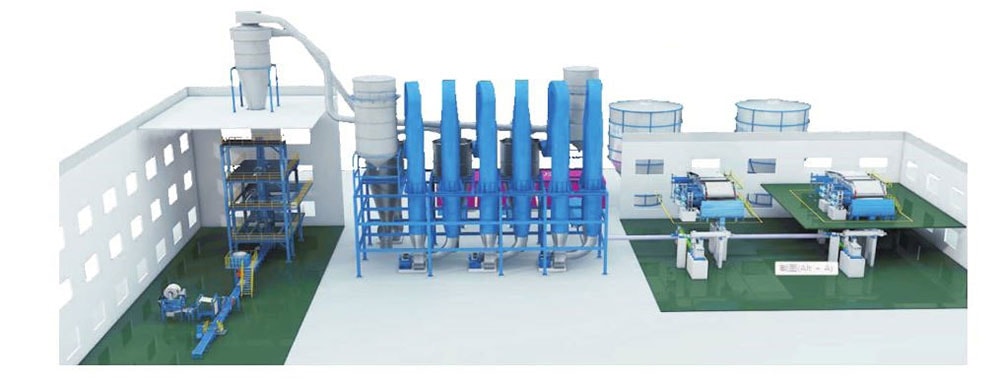
Due to the short storage time of the pulp, it can’t withstand long-distance transport. We have designed and developed pulp dry system to solve these problem. After the flash drying, the dry pulp block can be stored for a long time, which solves the problem that the wet pulp sheet only can be stored for short time or the pulp would be deteriorated over a period of time. And the dry pulp block can be transported over a long distance, thereby expanding the sales area of the products. Compared with the conventional pulp machine, the flash drying system has less damage to the fiber during the drying process, and the physical strength of the produced pulp is high. In addition to the application of traditional wood pulp and other virgin pulp fibers, it is more suitable for the drying of waste paper pulp, of which fiber strength is low; after the pulp is pressed into a pulp block, the unit volume density is high. The transport cost is lower than the cost of pulp sheet produced by traditional pulp machine.
- Pulp Pre-treatment System
First, the pulp passes through twin wire press, and the pulp consistency is increased from 3-5% to 45-48%. The pulp sheet output from the twin wire press enters into the shredding screw, and the pulp sheet is broken into small pieces. Then pulp enters to the fluffer. In the fluffer, the contact area is increased by rotor disc and static disc, which are with teeth, so as to achieve the most effective thermal drying, then the fluffered pulp is sent to the flash drying section. - Pulp Drying System
The heating source provides the heat energy, and the air is introduced into the heat exchanger through the fan, then it forms hot wind through heating exchange. Under the action of the fan, the hot wind blows up the fluff fibers to the high temperature drying stage. Through the three-stage drying tower, under the strong pulsation of high temperature difference and high humidity difference, the water evaporates strongly during the lifting, and the "flash drying" is completed. - Exhaust Gas Treatment System
During the flash drying, the evaporated mixture of humid air and the pulp fibers enter into the cyclone separator, which separates the pulp fibers and the humid air, and the separated pulp is sent to the next drying stage. The humid air is filtered in the scrubber then discharged to the atmosphere. - Pulp Slab Press
After three stages of flash drying, the pulp is sent to a cooling tower for cooling and further separation. The pulp out from bottom of the cooling tower enters into the feeding device of the slab press and is pressed into a pulp block. The dryness of the pulp block can reach 85%-90%. The exhaust device of the slab press is composed of negative pressure fans, and the discharged air enters the air filter chamber for filtration and the filtered air is charged out. The pulp block out from the slab press is sent to the subsequent sections for baling, storage and transportation. After the flash drying, the dry pulp block can be stored for a long time, which solves the problem that the wet pulp sheet only can be stored for short time or the pulp would be deteriorated over a period of time. And the dry pulp block can be transported over a long distance, thereby expanding the sales area of the products.